The phosphating process is a process in which a phosphate chemical conversion film is formed by chemical and electrochemical reactions. The formed phosphate conversion film is called a phosphating film. The main purpose of phosphating is to provide protection for the base metal and prevent the metal from being corroded to a certain extent; to be used as a primer before painting to improve the adhesion and corrosion resistance of the paint film layer; and to reduce friction and lubricate in the metal cold processing process.
1. Anti-rust phosphating process
The early application of the phosphating process is rust prevention. The steel parts are treated with phosphating to form a phosphating film, which plays an anti-rust role. The rust-proof period of the workpiece treated with phosphating can reach several months or even several years (for oiled workpieces). It is widely used for rust prevention during process, transportation, packaging, storage and use. The main types of anti-rust phosphating are iron phosphating, zinc phosphating and manganese phosphating.
1 The main bath liquid component of iron phosphating is ferrous phosphate solution, which does not contain oxidizing accelerators and has high free acidity. The treatment temperature of this iron-based phosphating is higher than 95°C, the treatment time is more than 30 minutes, the phosphating film weight is greater than 10g/m2, and it has the dual functions of rust removal and phosphating. This high-temperature iron-based phosphating is rarely used because the phosphating speed is too slow.
2 Manganese-based phosphating has the best performance as an anti-rust phosphating. The microstructure of the phosphating film is densely packed with particles. It is the most widely used anti-rust phosphating. It can be added or not with an accelerator. If nitrate or nitroguanidine accelerator is added, the phosphating film formation speed can be accelerated. Usually the treatment temperature is 80-100°C, the treatment time is 10-20 minutes, and the film weight is more than 7.5 grams/m2.
3 Zinc-based phosphating is also a widely used anti-rust phosphating. Nitrate is usually used as an accelerator. The treatment temperature is 80-90°C, the treatment time is 10-15 minutes, the phosphating film weight is greater than 7.5g/m2, and the phosphating film microstructure is generally a needle-like densely packed type.
4 General process flow of rust-proof phosphating:
Degreasing and rust-removing - water cleaning - surface adjustment and activation - phosphating - water cleaning - chromate treatment - drying - grease or dyeing
5 Workpieces treated with strong alkali and strong acid will cause the phosphating film to coarsen, and surface adjustment and activation can refine the grains. Zinc phosphating can be adjusted with oxalic acid and colloidal titanium. Manganese phosphating can be activated with insoluble manganese phosphate suspension. Iron phosphating generally does not require adjustment and activation. The phosphating workpiece can be greatly improved by chromate sealing, and the rust resistance can be improved by several or even dozens of times after oiling or dyeing.
2. Wear-resistant, friction-reducing and lubricating phosphating process
1 For workpieces such as engine piston rings, gears, and refrigeration compressors, it not only bears a primary load, but also has motion friction, requiring the workpiece to reduce friction and resist wear. Manganese phosphating film has high hardness and thermal stability, can resist wear, and phosphating film has good friction-reducing and lubricating effect. Therefore, it is widely used in piston rings, bearing supports, compressors and other parts. This type of wear-resistant and friction-reducing phosphating treatment temperature is 70-100℃, the treatment time is 10-20min, and the phosphating film weight is greater than 7.5g/m2.
2 In the cold processing industry, such as: pipe connection, wire drawing, extrusion, deep drawing and other processes, the phosphating film is required to provide friction-reducing and lubricating properties. Zinc phosphating is generally used. First, the zinc phosphating film forms a zinc stearate layer with good lubricity after saponification. Second, the zinc phosphating operating temperature is relatively low. Phosphating treatment can be carried out at 40, 60 or 90℃. The phosphating time is 4-10min, sometimes even tens of seconds. The phosphating film weight requirement is ≥3g/m2.
The process flow is:
A Wear-resistant and friction-reducing phosphating Friction-reducing and lubricating phosphating (cold processing)
B Degreasing and rust removal Degreasing and rust removal
C Water cleaning Water cleaning
D Manganese-based phosphating and zinc-based phosphating
E Water cleaning Water cleaning
F Drying Saponification (sodium stearate)
G Lubricating grease Drying
III. Phosphating process before painting
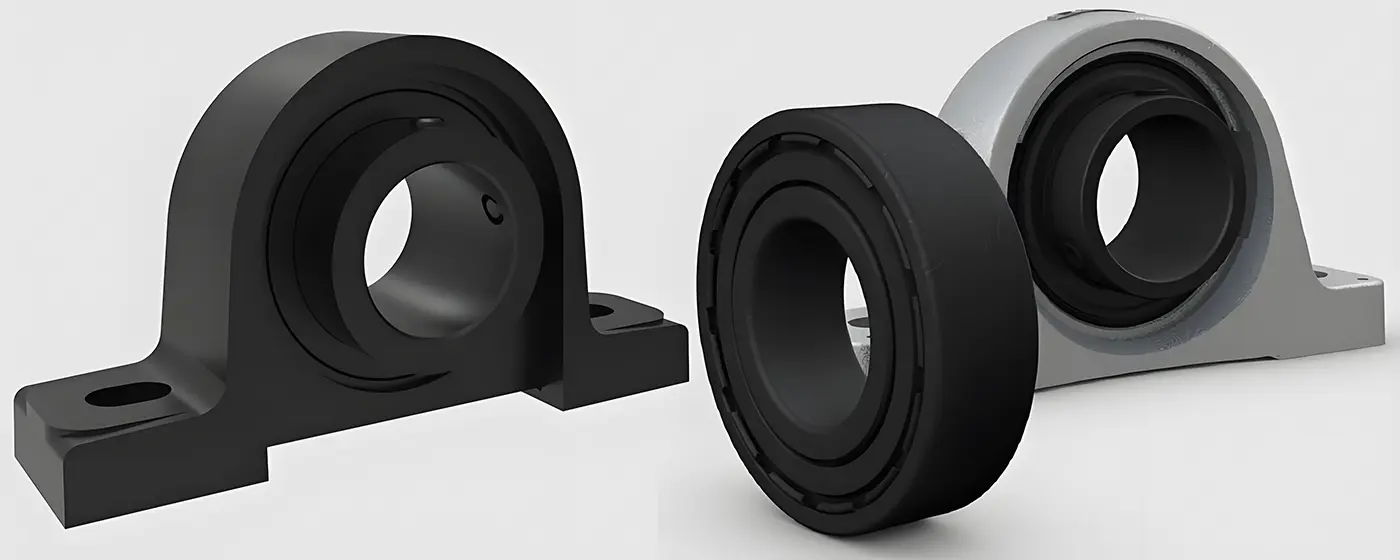
1 Phosphating treatment before applying primer will improve the adhesion between the paint film and the base metal, improve the corrosion resistance of the entire coating system; provide protection between processes to avoid secondary rust. Therefore, the primary problem of phosphating before painting is that the phosphating film must have excellent matching with the primer, while the rust resistance of the phosphating film itself is secondary. The phosphating film is fine and dense and thin. When the phosphating film is thick, it will have a negative effect on the comprehensive performance of the paint film. The selection of phosphating system and process is mainly determined by: workpiece material, oil rust degree, geometry; time interval between phosphating and painting; primer type and construction method and related site equipment conditions.
2 Generally speaking, low carbon steel is easier to phosphate than high carbon steel, and the phosphating film has better performance. For rusty (oxidized) workpieces, they must go through the pickling process, and the workpieces after pickling will bring a lot of trouble to phosphating, such as rust and yellowing between processes, removal of residual acid, and coarsening of the phosphating film. The workpieces after pickling generally need to
3 In intermittent production occasions, due to conditions, phosphating workpieces must be stored for a period of time before painting, so the phosphating film itself is required to have good rust resistance. If the storage period is more than 10 days, medium-temperature phosphating should generally be used, such as medium-temperature zinc, medium-temperature zinc-manganese, medium-temperature zinc-calcium, etc. The thickness of the phosphating film should preferably be between 2.0 and 4.5 g/m2. The workpieces after phosphating should be dried immediately, and should not be dried naturally to avoid rust in the gaps and welding points. If the storage period is only 3 to 5 days, low-temperature zinc and light iron systems can be used for phosphating, and the drying effect will be better than natural drying.
IV. Phosphating properties
1 Corrosion resistance
It has good corrosion resistance in the atmosphere, mineral oil, vegetable oil, benzene, and toluene, but poor corrosion resistance in alkali, acid, and water vapor. It still has certain corrosion resistance at 200-300℃, and the corrosion resistance of the film layer decreases significantly when the temperature reaches 450℃.
2 Special properties
Such as increased adhesion, lubricity, and friction and wear resistance.
V. Phosphating detection
1. Phosphate film inspection
① Appearance inspection
The phosphate film should be a uniform, continuous, and dense crystal structure when observed by the naked eye. There should be no residual blanks or rust stains on the surface that have not been phosphated. Due to different pre-treatment methods and effects, phosphate films of different colors are allowed, but brown is not allowed.
②Corrosion resistance inspection
A Immersion method: immerse the phosphated sample in a 3% sodium chloride solution, take it out after two hours, and it is qualified if there is no rust on the surface. The longer the rust appears, the better the corrosion resistance of the phosphating film.
B Drop method: At room temperature, drop the blue dot reagent on the phosphating film and observe its color change time. The color change time varies with the thickness of the phosphating film. Thick film > 5 minutes, medium film > 2 minutes, thin film > 1 minute.
2. Acidity
A Determination of free acidity
Use a pipette to draw 10 ml of the test solution into a 250 ml conical flask, add 50 ml of distilled water, and add 2-3 drops of methyl orange indicator (or bromophenol blue indicator). Titrate with 0.1mol/l sodium hydroxide standard solution until the solution turns orange (or titrate with bromophenol blue indicator until the solution turns from yellow to blue-purple), which is the end point. The number of milliliters of sodium hydroxide standard solution consumed is the free acidity point of the titration.
B Determination of total acidity
Pipette 10 ml of test solution into a 250ml conical flask, add 50ml of distilled water, and add 2-3 drops of phenolphthalein indicator. Titrate with 0.1mol/l sodium hydroxide standard solution until the solution turns pink, which is the end point. The number of milliliters of sodium hydroxide standard solution consumed is the total acidity point of the titration